This article reflects the opinion and analysis as well as information collated by AE Research Management Sdn Bhd, and does not constitute an investment advice or recommendation
It was once said that a single drop of impurity in an Olympic-sized swimming pool would ruin a batch of photoresist used in semiconductor fabrication. That was 20 years ago when the industry relied on deep-UV lithography. Today, for cutting-edge products, the acceptable impurity level is closer to a single drop in 1,000 Olympic pools, or parts-per-trillion (ppt). These highly specialized chemicals, dominated by Japanese chemical suppliers, are the result of years of collaborative development to achieve a custom-made product, specifically for each customer. But how did Japan become such a dominant player in this field?
Chemical Industry Development
Japan’s chemical industry began in the early 1900s, producing basic chemicals for fertilizers and textile bleaching/dyeing like any other countries. However, the major shift occurred after World War II, driven by the global transition to fossil fuels. The oil and petrochemical processing industries, led by companies like Idemitsu Kosan, Mitsubishi Chemical, and Sumitomo Chemical, fueled Japan’s rapid industrial and economic growth. Given the substantial investment and long-term returns required for oil refining and petrochemical plants, only large corporations could make such investment.
As a result, numerous mid-sized companies emerged to fill in the gap for small and niche market, specializing in refining and purifying solvents, synthesizing polymer for precision applications such as pharmaceutical and semiconductor production process. A typical example is the photoresists used in semiconductor lithography to etch the transistor circuits onto the silicon wafer (chart below).
Photolithography Process for Semiconductor Front-end Fabrication
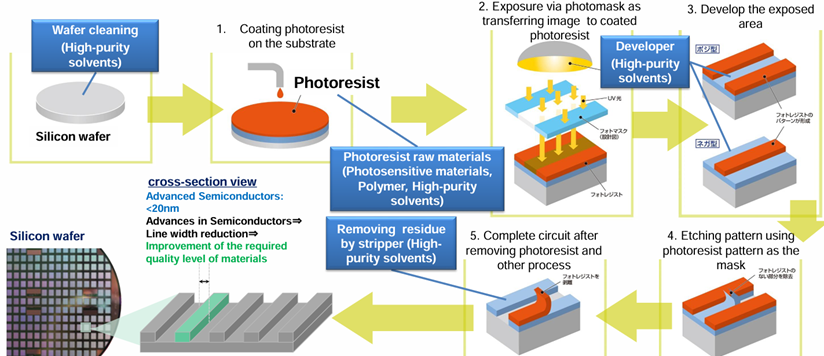
Source: Toyo Gosei
Tokyo Ohka Kogyo (TOK) was the first Japanese company to successfully manufacture photoresists, back in 1968, marking the start of a Japan photoresist journey. TOK continued to develop resist for g-line and i-line lithography, coinciding with Japan’s memory chip dominance in the 1970s and 1980s. During this period, the oil shocks also spurred Japanese petrochemical companies, particularly mid-sized ones, to develop derivative and higher-value chemical products for competitive advantage. For instance, JSR, initially focused on synthetic rubber and polymer, entered photoresist production in 1979.
But even as semiconductor production began to relocate from Japan in the 1990s, and despite the technology transition from i-line and g-line to KrF and ArF resists, Japanese companies retained their dominant position in the fine-chemistry market – Japanese suppliers still control over 90% of the global market for semiconductor photoresists. The question is how?
Understanding the Chemistry Challenges
As frequently noted, the semiconductor industry advances through gradual technological evolution, not rapid revolution, and this is especially true for semiconductor chemicals for several reasons.
The semiconductor chemicals are custom-made with iterative fine-tunings, requiring two to three years of collaborative development between suppliers and customers. This process fosters strong supplier-customer trade relationship, leading to a deep understanding of chemical reactions and accumulated library. The final product is a proprietary chemical formulation, or ‘black box’ recipes.
Photoresists ‘black box’ consists of photosensitive materials, resins (polymers), solvents, and additives. The ratio and selection of materials are constantly evolving around the chip structure and materials inside. Crucially, these high-end chemical recipes are primarily held by dominant Japanese chemical makers and their closely-tied mid-sized partners (see graphics below on photoresist supply chain)
Semiconductor Photoresists Supply Chain – Key Players
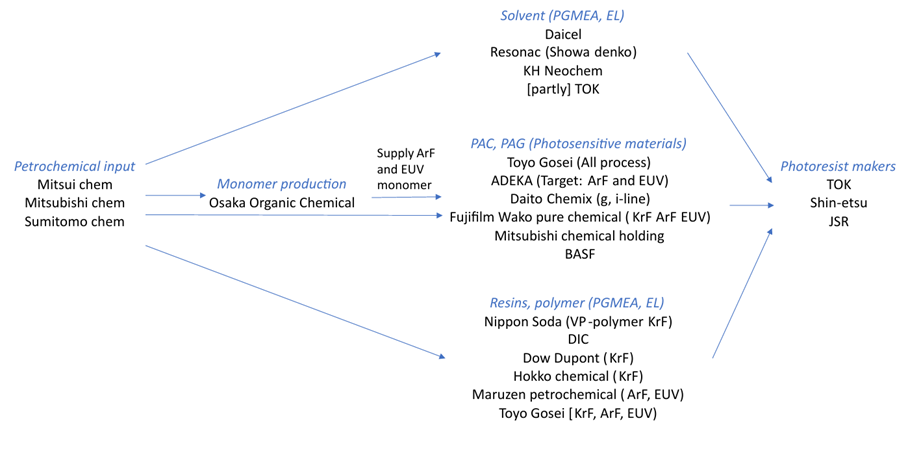
Source: AE Research Management
For example, Osaka Organic Chemical (OOC) supplies 70% of the monomer resins for ArF lithography, while Toyo Gosei controls 60% of the photosensitive materials market for both KrF and ArF. Given that EUV (extreme ultra violet) photoresists utilize a similar resist system, Toyo Gosei has already leveraged its existing library to capture 60-70% of the photosensitive materials of the most advanced EUV resist system. OOC is also developing a resin to be used in EUV resist as well.
Nonetheless, the tight relation and long-development time also acts as a double-edge sword, resulting in a slower return-on-investment. Lintec, a backend adhesive and tape maker, spend as long as 2-4 years’ time to codevelop the specification of tape with semiconductor fabs enduring the long development cost, waiting for its products to be put in the production line. But once the products are finalized, it can be hard to swap out. And the profit margin can reach up to 40-50% in high demand environment.
Reverse Engineering Will Not Succeed
The barrier to entry cannot be overcome though reverse engineering. As one photosensitive materials manufacturer explained, they maintain a library of over 100 product variations to exchange context with customers. Attempting to reformulate these chemical combinations is not only difficult but potentially uneconomical, given that the resulting formulation may be specific to only a single lithography exposure process.
Ultimately, knowing the chemical formula alone is insufficient unless it can be manufactured at a satisfactory level of quality – or at high-purity.
While extreme purity is consistently emphasized across all chemical companies, the technological details itself remain highly secretive. For instance, the closest available information describes how CMP abrasive materials utilize water to separate particles by size. However, this is merely ‘classification technology’, and the crucial ‘purification’ of impurities remains a proprietary technology known to only that chemical maker. This secrecy sometimes extends to the production equipment, which undergoes rigorous customer certification before operational use and is often dedicated solely to manufacturing these specialized products.
Lastly, the resilience of the Japanese chemical industry is worth mentioned here. Fine chemicals, produced in small quantities with diverse inventory libraries, present challenges to achieving economies of scale. This inherently creates a barrier to operate efficiently and profitably. However, due to the well-established nature and low-leverage balance sheets of Japanese mid-sized chemical companies, they are able to effectively execute their business model, and provide crucial products within their specialized chemistry competencies.