This article reflects the opinion and analysis as well as information collated by AE Research Management Sdn Bhd, and does not constitute an investment advice or recommendation
Stocks associated with fossil fuel have been derated to distressed valuations, due in part to the wholesale shift towards ESG-focused investing by global investors in recent years.
Yet, the irony is that many of the mission-critical technologies required for a true migration to a zero-emission world, depend on the R&D efforts undertaken by these companies. In this article, we will discuss examples of scientific breakthroughs by companies with fossil-fuel legacy which may be pivotal to wider adoption of clean energy sources.
Solid-state lithium batteries for Electric Vehicles (EVs)
Lithium-ion batteries (LiB) has undeniably become a part of our daily lives for decades in applications like smartphones and watches. However, nothing fuels the need for a next-generation batteries like EVs (to put simply, an electronic device with a thousand smartphone batteries combined!).
Existing LiB technologies are fast approaching their scientific limits in terms of energy density and also safety issues associated with flammable organic electrolytes. A shift to solid-state battery (SSB) which are energy-denser, faster-charging, and safer will solve the liquid electrolyte problem.
The adoption of SSBs depends largely on the challenging development of solid-state electrolyte materials such as ceramic (oxides, sulfide, and phosphate) or solid polymer. The sciences to develop such materials is often traced to companies with fossil-fuel lineage.
Taking sulfide-based SSBs as an example, Idemitsu Kosan has already possessed the technology to handle the toxic sulfide substance, a byproduct of petroleum refining, and developed them into the solid-state electrolyte. The company demonstrated high ionic conductivity of Li2S-P2S5 solid electrolyte well over a decade ago, and recently started its mass production in Chiba in 2021. This humidity-sensitive material is difficult to work with and even more costly to build a manufacturing line without proper know-how.
Compared to sulfide-type, oxide-based ceramic is not a toxic substance, and can easily be integrated into conventional manufacturing line. However, oxide also has its technical issue in terms of the interface formation within the material itself and with the electrodes (anode & cathode). Companies such as NGK Spark Plug which supply emission control systems for internal combustion engines, can apply their deep knowledge in the ceramic forming process to develop non-sintered ceramic electrolytes for EV’s batteries.
Hydrogen Fuel Cells
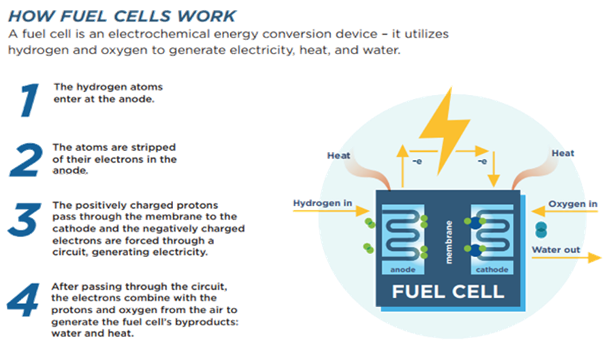
Source: FCHEA
An even more environmentally friendly energy source than LiB, is the hydrogen fuel cells – a device that generates electricity through an electromechanical reaction (see graphics above), not via combustion and does not need to be periodically recharged like batteries. The input is hydrogen and air, and the output is simply electricity, water and heat.
Key obstacles to wider adoption is durability and cost. Given the economics gap, fuel cell vehicles will take off more slowly that LiB-powered light vehicles. Instead, we expect fuel cells to gain traction in stationary power supply system (for businesses & households) and also in heavy transportation such as trucks and trains.
The fuel cell structure consists of an anode, a cathode and an electrolyte. There are various fuel cell technologies defined by their electrolyte type – polymer electrolyte membrane fuel cell, phosphoric acid fuel cell and solid oxide fuel cell (SOFC) are the most common. SOFC used a hard, non-porous ceramic compound as the electrolyte. SOFC has a much higher efficiency compared to other fuel cells and also does not require expensive precious metal catalysts (and associated system) to operate.
The NGK/Morimura Group of companies have resolved to combine their ceramic sciences capabilities to address the durability and cost of SOFC. Much of the work revolves around advanced ceramic laminating and bonding techniques to downsize the fuel cells stacks, and also testing technique to ensure durability of the materials (such as 10 years of use under operating temperatures of 700-1000 deg C).
Hydrogen Supply Infrastructure
In order to be green, the hydrogen source itself must also be as carbon-free as possible.
Hydrogen can be produced from hydrocarbon cracking, plus a carbon capture system that reduces CO2 by 90%. NGK Insulators has developed one of the largest zeolite membranes that efficiently separate CO2 even at high CO2 concentrations, pressures and temperatures.
Alternatively, truly green hydrogen can be produced via electrolysis of water, using electricity from renewable energy sources such as offshore wind farms. Such infrastructures will require the heavy fabrication capabilities of offshore oil-and-gas engineering companies such as Hyundai Heavy Industries.

Source: Hyundai Heavy Industries
Like natural gas, the bulk transportation of hydrogen must be in liquid form. The temperature at which hydrogen becomes liquid is minus 253 deg C, even lower than natural gas. Inevitably, Nikkiso Inc and other companies with cryogenic technologies for LNG, will play pivotal role in the transportation logistics of hydrogen in the future.